Working Metal
4D Spheres: Cast Iron, Aluminium, Bronze or Stainless Steel
Normally metal needs cutting grinding and polishing, and days of finishing to achieve its final shape. Metal in its very making is a work of imagination. It arrives as molten so needs a mould to form a shape as it cools.
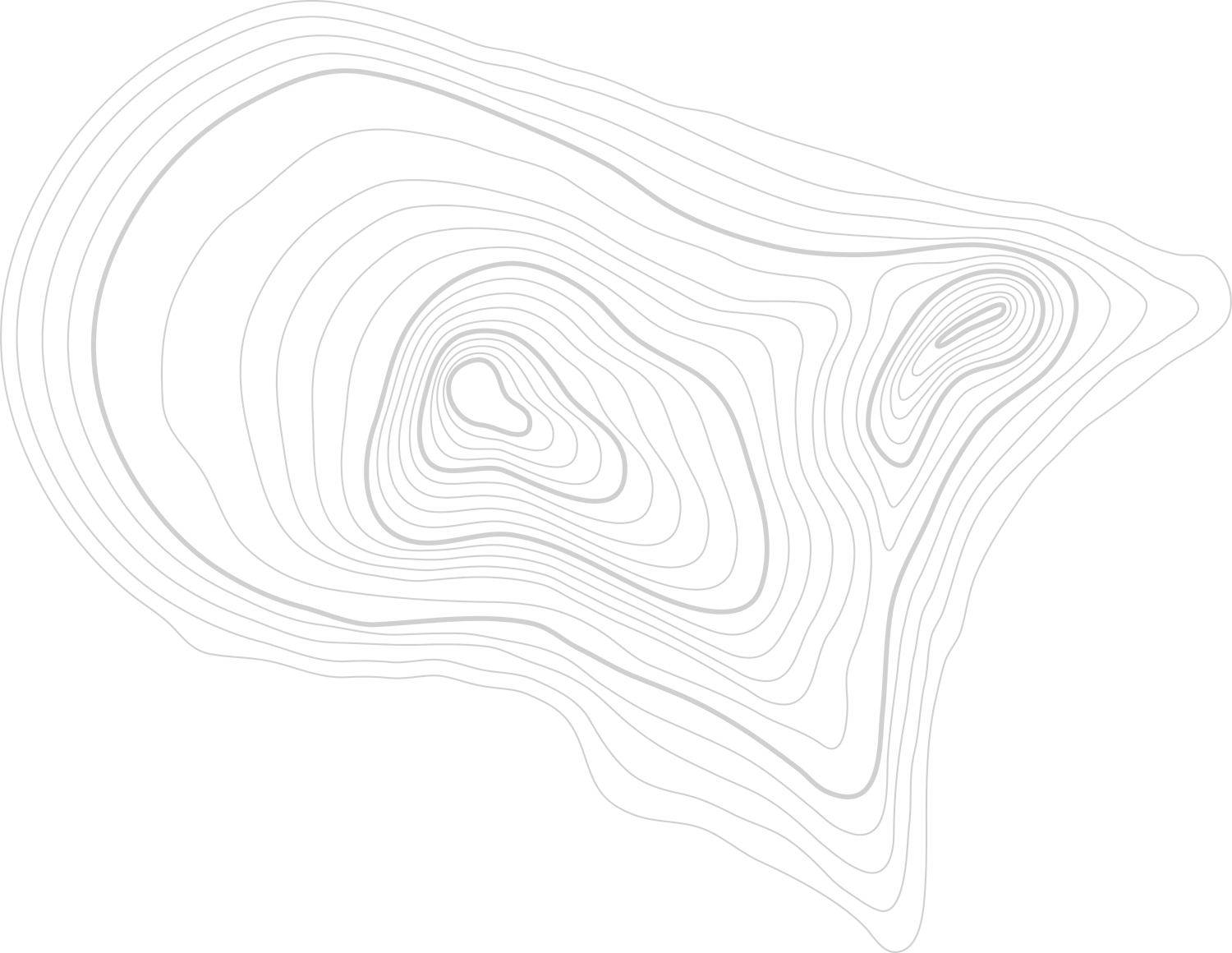
Visiting the local foundry in Hayle Cornwall to see white-hot metal poured into your hollowed mould, the idea's success hangs entirely on your conception.
Perhaps here, the creative process is most directly expressive; whatever is in your mind is visible in the eye of the beholder.
Further west at Geevor is a well-laid-out history of tin and copper production in Cornwall, from the earliest to 1990, some two thousand years ago. Initially, from alluvial deposits, the heavier metal particles could be manually panned out; later, as exposed lodes were exhausted, mining went underground.
Valuable in itself, tin could be mixed with copper to form bronze, which is hard enough for tools. Imagine the very first discovery of copper, as last night’s fire cooled.

“Melted, pooled from a fire.
Not for sword or tool
Polished to his heart’s desire
A mirror to show his love
Being first love’s fool.”
— Samvado
In the wrong ways of history, we’re told bronze was first seized upon for weapons, but in the unpopulated early world, strangers were wanderers, not enemies. The tin trade from Cornwall was Europe-wide, a seeming cooperation rather than competition, as much for expressing beauty as tools.
In London, my Dad took me to see the Shot Tower before it was demolished. Standing 50m high, molten lead, when dropped through a sieve from the top, would form perfect spheres to cool and harden as they fell into the water below. On Reflection from 2D to 3D, add imagination.